История русского металла и кокса
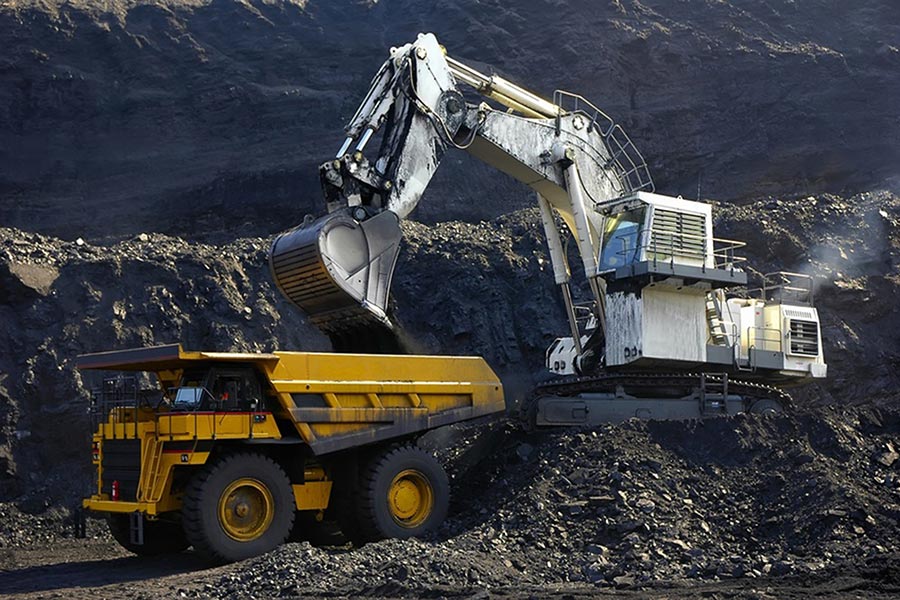
Урал исстари располагал богатейшими древесными и минеральными ресурсами. Обилие ценнейших руд и лесов открывало здесь большие возможности для металлургического производства.
Были и местные традиции железоделательного ремесла. Еще древние обитатели Перми Великой в VIII — IX вв. имели хорошо развитый промысел для получения сыродутного железа. Коренные жители Пермского края, которых русские летописи называли заволоцкой чудью (ныне это народ коми), оставили после себя столько следов металлургической деятельности, что В.И.Геннин, посылая в начале XVIII в. рудознатцев для поиска руд, давал им такую инструкцию: «Сыскать рудники старых чудских копей... понеже старинны люди не даром тамо промышляя, но знатно руду добывали».
В течение XV – XVII вв. происходило постепенное заселение русскими Урала и началось освоение его минеральных богатств. Территории Урала вошли в состав Российского государства, а численность русского населения к концу XVII в. достигла 200 000 чел.
Существование разбросанных по Уралу «чудских копей» не прошло бесследно. Они явились верными показателями месторождения руд. Когда на Урале появились первые русские промышленники и стала развиваться деревенская промышленность, то «чудские копи подали повод промышлять о заведении рудокопных промыслов».
Первые, зарегистрированные писцовыми книгами, железные крестьянские промыслы на Урале появляются в начале XVII в. Писцовая книга Кайсарова 1623 г. указывает, что на реке Каме, в устье реки Обвы, в слободке Слудке были две кузницы, в которых делали кричное железо, добывая руду на реке Косьве
В середине XVII в. в Чердынском уезде на «Красном бору» существовал «государев железный завод». Он имел одну домницу с двумя горнами и двумя молотами.
В 1628 г. к тобольскому воеводе Воину Корсакову от местного жителя Урала поступило сообщение о железной руде, найденной на реке Нице. На место находки был послан тобольский боярский сын Иван Шульгин, который осмотрел руду и привез ее образцы. Эти образцы были направлены на испытание в Москву, а оттуда на Урал поступил приказ о возведении завода.
Предприятие, построенное в 1631 г., имело лишь сыродутные горны с ручными мехами. Домны на нем отсутствовали. Не было вододействующих мехов и молотов, уже использовавшихся тогда в западноевропейской металлургии. Так возник прадед уральской и вообще русской металлургии — Ницинский же-лезоделательный завод. Работал он успешно, сгорел в 1637 г., но был отстроен заново и существовал еще лет сорок.
В 30-х гг. XVII в. во внутренних районах России началась постройка металлургических заводов. Первый тульский завод был основан голландцем А.Д.Виниусом в 1632 г. Впоследствии в компанию с ним вошел боярин Б.И.Морозов, глава правительства царя Алексея Михайловича. Однако Морозов вскоре вышел из предприятия, и в дело вступили голландец Филимон Акема и датчанин Петр Марселис, которые позднее построили на севере Олонецкие заводы имевшие характер мануфактуры. Во главе предприятия стоял крупный промышленник — представитель верхушки торгово-промышленного класса. На заводах существовало разделение труда, хотя не всегда последовательно и полно проведенное. Здесь имело место применение как крепостного, так и наемного труда, главным образом среди немногочисленных квалифицированных работников.
Заводчики получали привилегии, освобождались от пошлин, имели монопольное право на данное производство и обеспечивались правительством рабочей силой. Со своей стороны правительство опекало и регламентировало производство, что находило свое отражение в жалованных грамотах владельцам производств.
В дальнейшем заводы строят как казна, так и частные предприниматели, главным образом иностранцы, переехавшие в Россию, — Виниус, Марселис, Акема, Меллер, Бутенант и некоторые русские дворяне. В XVII в. они основывают свыше двух десятков железных заводов под Москвой и под Тулой, в Олонецком, Вологодском и других краях.
Следует отметить, что для постройки этих металлургических заводов часто привлекались уральские мастера.
Несмотря на появление своих металлургических заводов, металла в стране не хватало, Россия еще долго продолжала покупать часть железа за границей, что имело место в течение всего XVII в. Так, только в 1629 г. казна выписала 25 тыс. пуд. пруткового железа из Швеции Импортное железо стоило дорого, цены на него постоянно росли. Так, в 1693 г. пуд шведского железа в Москве стоил 42 коп., в 1700 г. – 43 коп., а в 1701 г. уже 80 коп.
Большая роль в строительстве крупных по тому времени металлургических предприятий принадлежала государству. Участие государства выражалось по-разному: или завод строился за счет казны (Пыскорский, Алатский, Олонецкий), или казна оказывала денежную помощь предпринимателям, выделяла рабочую силу, приписывая к заводу государственных крестьян.
Поскольку вода была основным источником энергии, заводы строили на берегах небольших запруженных рек впадающих в большие реки, служившие кроме источника энергии транспортными артериями.
В XVIII в. в русской металлургии произошел грандиозный скачок, и заняла она одно из первых мест в мире по производству железа. На Урале были найдены богатые залежи железной руды. Сочетание оказалось на редкость удачным: бескрайние, нетронутые леса, реки, на которых можно строить плотины, и горы руды с малым содержанием серы и фосфора.
Первые уральские заводы с доменными печами были построены на реках Каменке, Нейве и Алапаевке. 15 октября 1701 г. доменная печь Каменского завода выдала первый уральский чугун, а спустя месяц начал действовать доменный цех Невьянского завода. Поэтому именно 1701 г. считается годом начала уральской промышленной металлургии.
В 1723 г. на Екатеринбургском, Уктусском и Алапаевском казенных заводах трудовые затраты на тонну чугуна с учетом куренных и горных работ составляли 63 человеко-дня, а в условиях ремесленного производства они повышались до 150 человеко-дней. Производительность труда на заводах была выше в 2,4 раза. Расходы руды на тонну чугуна в условиях ремесленного производства составляли 4,3 т, а на заводах — 3 т, то есть на 30% меньше. Расход угля на тонну металла в условиях ремесленного производства составлял 6 т, а на заводах - 3,4 т, т.е. на 43% меньше.
Богатейшие топливные ресурсы, разделение труда, позволявшие в условиях крепостного права принудительно привлекать рабочую силу, поддержка железоделательных заводов со стороны государства - все это способствовало быстрому вытеснению ремесла и превращению Урала в основной металлургический центр России. Заводы Урала работали на широкий внутренний и внешний рынок. Действовали они по принципу максимального обеспечения всех звеньев производственного цикла за счет собственных ресурсов. Таким образом, в Петровскую эпоху в крае был создан новый металлургический район, превосходящий по своей мощи все старые районы России.
В течение всего XVIII в. металлургия Урала сохраняла ведущее положение в черной металлургии России. Особенно большого развития достигла в конце XVIII в., заняв по выплавке чугуна первое место в мире. В 1793 г. в России выплавлено 140 тыс. т чугуна, в Англии в 1790 г. — 80 тыс., во Франции в 1789 г. — 69 тыс., в Швеции в то же время — 67 тыс. т.
Высокое качество уральского железа вызывало большой спрос на него за пределами страны, особенно много железа вывозилось в Англию. В то время Россия имела самые большие доменные печи. Уже тогда здесь строились доменные печи круглого сечения, в то время как в Западной Европе еще преобладали печи четырехугольного сечения.
Производительность уральских печей, была выше европейских. Лучшие шведские домны давали в среднем за сутки З,3 т (около 206 пуд), В них на получение 100 кг чугуна затрачивалось 300—350 кг древесного угля, в уральских в два раза меньше, а по качеству уральский чугун не уступал шведскому. В 1770 г. одна доменная печь Нижнетагильского завода давала за сутки 500 пуд. чугуна.
Богатая руда, дешевый уральский лес и труд крепостных позволили получать дешевый и высококачественный металл. По рекам Чусовой, Каме, Волге, каналам Мариинской системы плыл уральский металл с фирменной маркой «Старый соболь», загружался в трюмы морских судов и обращался в чистое золото в конторах английских, немецких, французских компаний.
Марка уральского железа «Старый соболь» получила известность и признание во всем мире. Изображение на клейме имело глубокий смысл: железо «доброе и мягкое», как соболий мех. Уральскую продукцию с маркировкой демидовских заводов зарубежные потребители предпочитали всякой другой, и это весьма раздражало иностранных конкурентов. Случалось, попадались они с поличным за постыдным занятием - подделкой демидовского знака.
В 1833 г. в департамент внешней торговли Российской империи поступило донесение одного из русских консулов, что на Ионических островах – важном перевалочном пункте международной торговли железом – решительно предпочитают русский металл английскому или какому-либо иному. И вот английские заводчики, как сообщал консул, стали обманывать торговцев-покупателей, подделывая клеймо, которое кладется на русском железе после первой отковки.
Крыши старой части Лондона (Сохо), говорят, были покрыты в XVIII в. тагильским железом и до сих пор не текут. В конце XVIII в. «Старый соболь» занял ключевые позиции на мировом рынке. Из уральского сырья изготовляли в Англии знаменитую шеффилдскую сталь.
Таким образом, английская промышленная революция в XVIII в. была замешена на уральском древесно-угольном железе.
Нелегким был труд уральских рабочих. Немногие доживали до 40 – 45 лет. Прибыли Демидовых, как и других уральских заводчиков, росли на костях приписных крестьян, а уральский металл был закален на крови и поте работных людей.
И здесь была велика роль древесного угля или правильнее древесного кокса, который выжигался в кучах.
XVIII век. Уральские углежоги, обычно приписанные к тому или иному частному или государственному металлургическому заводу, еще осенью начинали заготавливать древесину на так называемых «дачах» - лесных угодьях, причем каждый завод имел свои «дачи».
На Урале распространение получил костровой способ, т.е. собственно то, что называлось кучным коксованием. Он предусматривал сооружение наземных сооружений — куч откуда и способ получил название кучного коксования или углежжения. Куча представляла собой сооружение типа «шалаша» 3 – 4 метров высотой и таким же диаметром. В центре кучи устраивался из дерева или камней канал для отвода дыма, сверху (по поверхности) куча засыпалась землей или глиной и обкладывалась дерном.
Для производства древесного кокса, который назывался древесным углем и предназначался для доменных печей, использовались стволы деревьев, в основном, хвойных пород, которыми изобиловал Урал.
Наибольшее распространение получили, по мере развития техники кучного коксования, две конструкции: «Уральский кабан» - куча, в которой стволы укладывались вертикально, но куча имела в длину больший размер, чем в высоту и «Суксунский костер», где стволы укладывались горизонтально один на другой как при постройке избы.
Углежог должен был обладать немалым опытом. Во-первых, сложной была укладка кучи с оставлением специальных каналов для прохода необходимого для горения воздуха и отвода дыма. Уложенные в кучу древесные стволы поджигались и частично сгорали. По цвету дыма углежог определял, какое количество воздуха нужно подавать, закрывая или открывая отверстия в засыпанной землей и глиной куче. Во-вторых, надо было вовремя остановить процесс, чтобы весь материал не выгорел, и получить максимальный выход целевого продукта..
Выход древесного угля от древесины в первых кучах, а этот способ не известно с какого времени использовался практически во всем мире, для получения кузнечного топлива составлял значительно меньше половины, а то и десятую часть. «Старый соболь» приносил большие прибыли заводовладельцам, но беспощадно уничтожались уральские леса. В конце XVIII в. горнозаводская промышленность Уральского региона «съедала» более 4 миллионов кубометров древесины в год, а в 1913 г. было переработано на древесный уголь 17 млн м3 .
Именно поэтому, стоящий у истоков уральской металлургии В.Н.Татищев требовал, чтобы, наряду с вырубкой леса осуществлялась его регулярное восстановление. Горнозаводская администрация не разрешала строить новые мощности, если было недостаточно леса для древесного угля.
Только маленький, по современным масштабам, Тагильский завод ежесуточно сжигал, например, в первые послереволюционные годы уголь, производимый с одного гектара леса. А современному Нижнетагильскому металлургическому комбинату, если бы он работал на древесном угле, надо было бы каждые сутки расходовать лес, занимающий площадь примерно полтора квадратных километра. Поэтому уже к середине XIX в. лес приходилось возить к «дачам» тагильских заводов за десятки верст.
Трудности усугублялись еще и тем, что ни в XVIII, ни в XIX вв. владельцы уральских заводов не задумывались о будущем заводов, об их техническом перевооружении, об улучшении условий труда рабочих на заводах. Заводы рассматривались только как источник доходов, они давали миллионы рублей прибыли, и эти миллионы целиком расходовались на великолепные дворцы, на пиры, на приобретение итальянских княжеских титулов.
Старело оборудование, падала производительность, но это мало волновало хозяев, которые по-прежнему занимались выколачиванием доходов.
Но все таки почти 150 лет становым хребтом российской металлургической промышленности был Урал.
В небольших по объему, малопроизводительных доменных печах, работающих на холодном дутье, получали чугун хорошего качества, при этом использовали древесный уголь, который выжигали в кучах, «коксующих» ценную уральскую древесину.
Интересно, что такая технология дожила на Урале до ХХ в. В музее техники Урала на Екатеринбургской «плотинке» есть фотография куч на Верхне-Уфалейском медеплавильном заводе, сделанная в конце Х1Х в. Конечно, кучи несколько усовершенствованы. Имеется постоянная каменная труба в центре, каменное основание, но в остальном – это та же куча.
В библиотеках Екатеринбурга есть соответствующие руководства издания 30-х и даже 40-х гг. ХХ в. о том, как в кучах выжигать древесный кокс. Особенный интерес эти руководства вызывали в период войны 1941 – 1945 гг.
Из-за того, что уральская металлургия XVIII – Х1Х вв., да и до начала 30-х гг. ХХ в., «базировалась» только на древесном угле, который, хотя и отличается очень низким содержанием такого вредного элемента как сера, и низкой зольностью, однако доменные печи, выплавляя чугун очень высокого качества, не могли увеличивать производительность, так как имели малый объем.
Древесный кокс (древесный уголь) имел крупный недостаток – малую прочность. Из-за этого доменные печи не могли расти в высоту, увеличивать полезный объем. Кроме того, лесов оставалось все меньше и меньше. И вопрос получения металлургического кокса из каменных углей для уральских домен становился все более актуальным.
Уголь на Урале был. Впервые каменный уголь был отыскан для заводских целей в 1797 г. в Камышловском уезде на р. Ирбите, а затем в 1802 г. на р. Пышме. Но угли эти были низкого качества и без примеси древесного угля не горели даже в кузнечных горнах. В 1820 г. здесь уже заложили 3 угольных прииска, но даже на богатейших Кизеловских копях добыча составляла всего около 100 тонн в год.
Уголь был во всем Уральском экономическом районе (по сегодняшнему делению это Свердловская, Челябинская, Пермская, Курганская, Оренбургская области, Башкирия и Удмуртия).
Первые опытные коксования в стойловых печах были проведены по инициативе владельца заводов Всеволожского, но дали отрицательные результаты.
Дело в том, что для получения металлургического кокса нужен не просто уголь, а обладающий специфическими особенностями – коксующийся уголь, который при нагревании без доступа воздуха до температуры 1000ºС, при 350 – 450ºС переходит в пластическое состояние и при дальнейшем нагреве дает проплавленный очень прочный материал – металлургический кокс. Таких углей очень немного. Всего 10 – 15% от общего количества. И вот с этими-то углями дело обстоит на Урале плохо.
Поскольку коксованию для получения металлургического кокса подвергается не только хороший коксовый уголь, а коксуется смесь углей, всегда проводились опыты по добавке небольшого количества уральских углей к шихте для коксования.
Добавлялись бурые угли, длиннопламенные, но эти опыты не дали положительных результатов. Пробовали использовать уральские антрациты и полуантрациты непосредственно в доменной плавке, но и эти опыты, проводившиеся в Х1Х в., не дали положительных результатов.
И вот «Старому соболю» англичанами был нанесен сокрушительный удар. На смену древесному углю в домны пришел каменноугольный кокс, и английский металл стали активно продавать на мировом рынке, а цена его была ниже уральского.
В Англии передел чугуна в сталь стоил в два раза ниже, чем в России.
Так продолжалось бы долго, если бы не были открыты месторождения железных руд в районе Кривого Рога, и не потребовался углеродистый восстановитель для получения металла из этой руды, который был в Донецком угольном бассейне.
Но объективности ради, следует отметить, что началу развития металлургии на Украине и вообще Юге России положил Урал.
Построенный в 1796 г. Луганский металлургический завод первенец южной металлургии долгое время работал на уральском чугуне. Но каменноугольный «русский кокс» начинался на Украине.
Особенности географического положения Кривого Рога: близость к речным и морским путям, удобство гужевого транспорта (в те времена имело немаловажное значение), большая плотность населения в том районе и отмена крепостного права (1861), давшая мощный толчок развитию капитализма в России, громадный резерв дешевой рабочей силы, способствовали развитию производства кокса на юге России. Лесов почти не было, а географическое понятие «Донецкий бассейн» уже начало заявлять о себе поставками угля для строившихся железных дорог. К этому времени здесь открыли месторождения известняков и огнеупорных глин. Условия для развития металлургии были идеальными.
Еще в 1795 г. имелись сведения о хорошей коксуемости донецких углей и возможности их применения для выплавки чугуна. Тогда горный инженер Иван Бриганцев писал: «железные руды, выплавляемые обожженным каменным углем, дают превосходных доброт чугун для отливок всех вообще военных орудий, снарядов и других вещей».
Коксовым производством в России заинтересовались иностранные фирмы. Первая промышленная установка из 50 печей системы Коппе была пущена на Украине при Веровском угольном руднике, недалеко от станции Государев Байрак Бахмутского уезда (Бахмут ныне г. Артемовск, Украина) Харьковской губернии. В дальнейшем коксовые установки строились в основном на территории нынешних Донецкой и Луганской областей. В 1870 г. в России уже выжигалось около 275 тыс. т каменноугольного кокса, в основном на установках при угольных шахтах. В основном это были стойла или пламенные печи Коппе.
Период становления металлургической и коксовой промышленности юга России характеризуется значительным участием иностранного капитала. Как грибы росли различные акционерные общества (русско-бельгийское, русско-французское, русско-английское и др.).
Это и определяло обстановку, которую описал писатель Александр Бек в повести «Доменщики» о знаменитом русском доменщике Михаиле Константиновиче Курако. «Все коксовые печи России построены иностранными компаниями – Генрих Копперс, Эванс Коппе, Оливье Пьетт, Семет Сольве и др.»
К концу XIX в., обращаясь к любой из фирм, владелец шахты коксующихся углей мог получать кокс практически без затраты капитала. Фирма строила коксовые печи за свой счет. Шахтовладелец доставлял уголь к печам и получал кокс. За выжиг кокса фирма опять-таки не брала ни копейки. Вознаграждением для нее был газ – «побочные продукты коксования». Фирмы имели миллионные прибыли.
Первая коксовая батарея с улавливанием химических продуктов коксования была также построена в Донбассе на Щербиновском угольном руднике в 1899 г.
Высокие стены ограждали коксовые заводы в Донбассе. Туда не пускали русских инженеров. Фирмы охраняли секреты коксовых печей. Все привозилось из-за границы. Фигурный огнеупорный кирпич и материал для связки, оборудование, специалисты, даже квалифицированные рабочие, не говоря о чертежах или секретах технологии.
И это неудивительно для тогдашней царской России. Ведь горел же, например, в топках кораблей русского военного флота английский уголь «кардиф» (по названию порта в Англии).
Пытались даже перевести уральскую металлургию на привозной английский кокс. Его должны были кораблями доставлять в Архангельск, а затем на лошадях перевозить на Урал.
На южных заводах франко-бельгийской фирмой и до и сразу после революции было построено много коксовых печей системы Коппе.
Даже после Великой Отечественной войны старые рабочие, работавшие на южных заводах и оставшиеся после эвакуации на Урале и в Сибири называли двери коксовых печей «лапортами» (от французского «ля-порт» – дверь), угольную башню – «турмой» (от французского слова «ля-турм»-башня).
Сейчас уже никто не называет газосборник «барильетом» (фр.), но в штатном расписании коксового цеха есть должность барильетчика (так называется рабочий, обслуживающий устройство для сбора и охлаждения коксового газа, расположенное наверху коксовых печей).
Очевидцы рассказывали, что академик Н.П.Чижевский, один из корифеев отечественной коксохимической промышленности, как-то шутил, побывав на заводе Донбасса в конце 20-х гг. ХХ в. Он предложил рабочую – женщину, которая заливала кокс водой, называть «ля-фам» (по-французски – женщина) по аналогии с лапортами, турмами, вольверами и др.
Только в конце Х1Х в. установки для коксования углей стали строить на востоке страны там, где имелись значительно большие, чем на Юге запасы углей.
В конце 80-х гг. XIX в. в Луньевке, на севере Пермской области, были построены две коксовые батареи системы Коппе – пламенные печи без улавливания химических продуктов коксования. Они предназначались для получения кокса из хорошо спекающихся углей Кизеловского бассейна, однако, поскольку эти угли характеризуются очень большим содержанием серы, весь кокс отправляли на медеплавильный завод, а для доменных печей не использовали. Печи были малопроизводительными, угля загружалось всего 1,83 тонны в одну камеру.
Этот небольшой завод интересен тем, что на нем была построена первая на Урале углеобогатительная фабрика (для снижения зольности угля) производительностью 130 тонн угля в сутки.
После остановки печей кизеловские угли продолжали коксовать в кучах и стойлах для нужд медеплавильной промышленности и кузнечного дела.
К 1909 – 1912 гг. относятся первые опыты промышленного коксования углей Кузнецкого бассейна. В этот период в кучах было выжжено 4150 тонн кокса.
Толчком промышленному развитию коксохимической промышленности, как на Украине, так и на Урале и в Сибири послужили события, отнюдь не мирные.
В 1914 г. началась первая мировая война. Металла и химического сырья для производства огромного количества вооружения в царской России не хватало. Не было в России и сырья для производства взрывчатки. Бензол, толуол, которые получали улавливанием их из коксового газа, выделяющегося при коксовании, везли из-за границы. Ведь из 5457 коксовых печей, выжигавших кокс в России, только 1008 были оборудованы устройствами для улавливания химических продуктов.
Крупный капитал, поборов косность царских чиновников, обратил свои взоры на восток. Уже в 1916 г. построенные в районе Кемерово стойловые печи выдали первый кокс.
В это время над проектированием крупного металлургического завода в районе Кузнецка работает большая группа талантливых инженеров-металлургов. Группу возглавлял знаменитый доменщик М. К. Курако. В проектировании коксохимического завода участвовал инженер И. И. Лоханский будущий автор одного из первых русских учебников по коксованию углей.
К 1916 г. производство кокса в России достигло 4,5 млн. т. Несмотря на то, что в Донбассе работали крупнейшие, по европейским масштабам, заводы Кадиевский и Брянский, коксохимическая промышленность России была крайне отсталой.
Производительность коксовых батарей также была очень низкой. На заводах преобладал ручной труд. Рабочие вручную открывали и закрывали двери печей. Загрузочный вагон по верху коксовой батареи также передвигался с помощью нескольких рабочих. Существовали ручные коксовыталкивающие машины. Охлаждали кокс тоже вручную, поливая его водой из ведер или в лучшем случае из шлангов. Не хватало контрольно-измерительной аппаратуры.
На коксовых батареях, находившихся поблизости от доменных печей и отапливающихся доменным газом, который содержал много ядовитого оксида углерода (угарный газ), применяли очень своеобразные приборы, сигнализирующие об утечке доменного газа.
Утечки случались очень часто. Угарный газ уходил через малейшую неплотность в стыках газопроводов, через трещины, неисправные клапаны и накапливался в тоннелях печных камер, приямках и других местах, где приходилось часто находиться обслуживающему персоналу. Поэтому в тоннелях коксовых батарей и на пультах управления стояли клетки с канарейками или белыми мышами, которые очень чувствительны к малейшим концентрациям оксида углерода. Как только канарейка или белая мышь начинали беспокоиться или падали, рабочие спешно покидали помещение.
Для строительства коксовых установок использовалось устаревшее оборудование. Коксовые установки строили из так называемого полушамота (бракованный шамот).
Для дореволюционного развития промышленности России характерно хищническое отношение к использованию природных богатств. Так, коксовались только лучшие по качеству угли. Мелкие классы хорошо коксующихся углей часто шли в отвал или на сжигание.
По условиям труда работа «коксовальщиков» была одной из самых тяжелых и изнуряющих. Рабочий день длился 12 час.
Побывавший в Юзовке (Донецк) летом 1897 г. писатель А.С.Серафимович в очерке «На заводе» писал: «То и дело из раскрытых камер вываливался горящий кокс, вдоль печи, на десятки саженей громоздились огромные огненные груды раскаленного кокса. Стоять возле них не было физической возможности, волосы подымались, трещали, скручивались, платье коробилось. Несколько рабочих в одних портах и рубахе подскакивали и, отворачиваясь, плескали из ведер воду на горящий кокс и сейчас же стремительно бросались прочь».
После революции молодое Советское государство получило в наследство технически отсталую промышленность. Началась гражданская война. Остановились водоотливные машины в шахтах, коксовые батареи.
Считают, что в 1918 г. производство кокса в России прекратилось. В литературе вообще нет данных о производстве кокса в 1918 – 1919 гг. По-видимому, в этот период на 49 заводах, существовавших до революции, не работала ни одна коксовая печь, ни одна домна. В Донбассе были взорваны не только мосты, но и цехи, и дымовые трубы заводов.
Многое мешало начавшемуся в начале 20-х гг. восстановлению промышленности: не хватало рабочих, продовольствия и рабочие уходили в деревню.
Вот как об этом пишет писатель А. Бек в рассказе «Последняя домна»: «Одна домна по всей стране продолжает кампанию, Старопетровская № 6, последняя печь Юга. Редкие огни над коксохимическим заводом. Мелкосортный стан катает ходкий крестьянский товар – уголок, шинку, обручик, кругляк… Она единственная продержалась летом 1921 г. до нового хлеба».
И все-таки на восстановленных коксовых печах Донбасса в 1921 г. было выжжено 102 тыс. т кокса. К 1927 г., то есть к началу первой пятилетки, были полностью восстановлены 19 заводов Донбасса. Характерная цитата из художественного произведения.
«Один американец, инженер, говорил, что у них в Америке очень удивляются специалисты-коксовики, как это мы можем строить коксовые заводы и даже, что уже совсем странно – получать на них кокс, годный для домен, когда у нас нет негров. Этого большевистского фокуса понять, они говорят, совсем не в состоянии». [1]
Вся страна совершала подвиг строительства новой индустрии. Строились новые заводы в Донбассе и Приднепровье. От Керчи до Кузнецка и Магнитки развернулось строительство металлургических гигантов, в состав которых органично входили коксохимические заводы. И в эти годы коксохимия пришла на восток нашей страны – на Урал и в Сибирь.
Еще Д. И. Менделеев писал: «Кузнецкий каменноугольный бассейн Западной Сибири представляет сумму всех благоприятных условий для успешного будущего развития обширнейшей железной промышленности, потому что в этих местах не только найдены громадные запасы превосходных железных руд, но и каменные угли, необходимые для их переработки».
В мае 1921 г. Совет Труда и Обороны (СТО) рассмотрел вопрос о развитии промышленности Кузнецкого угольного бассейна. В постановлении… СТО, 20 мая 1921 г., говорилось: «Работы по Кузнецкому бассейну, состоящие… в окончании постройки и оборудовании Кемеровского коксохимического завода с пуском первой батареи в 50 коксовых печей… признать работами ударными».
Интересна история этого завода, строительство которого было начато в районе села Щеглово недалеко от Кемерова. Начала его строить бельгийская фирма «Оливье Пьетт» еще до первой мировой войны, но революция и гражданская война помешали строительству.
19 сентября 1921 г. В.И.Ленин принял группу иностранных коммунистов во главе с голландским инженером С. Рудгерсом и американцами В. Хейвудом и Г. Кальвертом.
Эта группа создала на территории Кузбасса «Автономную индустриальную колонию» (АИК), которой и были переданы работы по строительству Кемеровского коксохимического завода. Здесь работали свыше 200 иностранцев и более 2000 местных жителей. 2 марта 1924 г. коксовая батарея выдала первый кокс, который был отправлен на заводы Урала и Сибири. Большинство колонистов потом разъехалось, но многие интернационалисты навсегда связали свою судьбу с Россией. Их опыт был использован в строительстве нового Кемеровского завода и коксовых батарей на Кузнецком металлургическом комбинате.
Этот комбинат начал строится на окраине старинного сибирского города Кузнецка одновременно с Магнитогорским металлургическим комбинатом.
Главным инженером Кузнецкого металлургического комбината был будущий академик И.П. Бардин, который еще до революции поработал в США на металлургических заводах Форда и имел немалый опыт. По его настоянию и был использован самый передовой в то время американский опыт и американское оборудование. Первые доменные печи и коксовые батареи начали работать практически одновременно с Магниткой. Кузнецкий металлургический комбинат (КМК) был одним из основных факторов, обеспечивших победу в Великой Отечественной войне.
В шестидесятые годы ХХ в. вблизи старого Кузнецка, переименованного в Новокузнецк был построен Западно-Сибирский металлургический комбинат, в составе которого имеется крупнейшее коксохимическое производство, а в 1978 г выдала кокс первая батарея последнего по списку коксохимических производств СССР Алтайского коксохимического завода, который расположен в городе Заринске в 100 км от столицы Алтайского края города Барнаула. В настоящее время это самый новый коксохимический завод России и всего СНГ.
В двадцатые годы ХХ в. шли дискуссии о судьбе металлургии Урала. Победило мнение, провозглашенное еще в плане ГОЭЛРО – создание Урало-Кузнецкого комбината. При этом учитывалось то обстоятельство, что на Урале имелись запасы отличных руд, а в Кузбассе – месторождения коксующихся углей: поезда везли в Кузбасс уральскую руду и возвращались обратно с углем.
С коксовых батарей начинался пуск новых заводов. Отсутствие собственного опыта в строительстве коксохимических заводов заставило первоначально воспользоваться технической помощью специалистов иностранных фирм. Но, несмотря на привлечение иностранных фирм для строительства коксохимических заводов, уровень европейской техники уже не удовлетворял требованиям становления промышленности. Поэтому в годы первой пятилетки широко использовался опыт американцев в строительстве крупных коксохимических заводов.
У американской фирмы «Беккер» была куплена лицензия со всеми материалами и чертежами на коксовые печи системы Беккер, которая стала основой для многих советских конструкций коксовых печей.
Опыт опытом, но ведь не было даже квалифицированных рабочих. Писатель Федор Панферов в своих знаменитых «Брусках» верно подметил момент, что даже для самых квалифицированных каменщиков – трубокладов и печников – отсутствие опыта работы с фигурным огнеупорным кирпичом вызывало большие трудности. И все из-за требований необычной для каменной кладки точности.
«На кладке из красного кирпича он весь был одной формы. А тут пятьсот восемьдесят шесть (!!) форм (марок)… Марки идут по номерам.
А у молодых мастеров хмурятся при каждой новой марке лбы: марку нужно знать, где и как положить, надо умело смазать материалом, смазать – положить так, чтобы не было ни одной самой незначительной щели, ибо скоро в печи разбушуется тысячеградусная жара, тогда газ выпрет наружу и печь выйдет из строя… Кладка должна быть точной, ни сантиметра в сторону».
Ошибся писатель. Не сантиметров, а миллиметров. Кладка коксовых печей самая точная каменная кладка технических агрегатов.
За период с 1927 по 1932 г. на юге СССР, теперешней Украине, было построено много коксовых батарей иностранными фирмами. Однако они неохотно раскрывали секреты строительства, не всегда передавали строительные чертежи. Так, например, представитель иностранной фирмы в Горловке после окончания строительства коксовой батареи демонстративно сжег все чертежи.
Большое внимание уделяется повышению качества кокса и химических продуктов коксования.
Достижения коксохимической промышленности в годы первой пятилетки нашли отражение в постановлении ЦК ВКП (б) от 2 октября 1932 г. о черной металлургии, гласящем «Заново создана, на основе передовой техники, коксовая промышленность».
В 1932 г. было пущено 9 доменных печей, в том числе 6 печей американского типа. А уже в 1934 г. в строй вступила коксовая батарея, построенная по отечественным чертежам Гипрококса из советских огнеупоров рабочими, инженерами и техниками треста «Коксохиммонтаж», созданного в 1931 г. Теперь можно было отказаться от помощи иностранных фирм. Это была большая победа, и все-таки это было только начало.
Построенные самые совершенные по тому времени доменные печи часто стали выходить из строя, плохо работали, мало давали чугуна, потребляя при этом огромное количество кокса. Доменщики справедливо бранили коксовиков, которые выдавали неравномерный кокс: то крупный, то мелкий, непрочный; при выпуске чугуна выносится коксовая мелочь, а бывает и «козел» угрожает – это значит, что отдельные участки объема доменной печи охлаждались, масса застывала и могла остановить «ход» печи .
Выходили из строя и коксовые батареи.
Закон работы коксовой батареи – это постоянство и равномерность. Только в том случае, если на коксовой батарее во всех отопительных простенках поддерживается заданная температура и если во всех камерах коксования угольная загрузка находится одно и то же время, можно рассчитывать на то, что кокс будет одинаковым всегда, то есть равномерным по качеству.
Но что делать, если в одном отопительном простенке температура на 100 градусов выше, чем в другом, или температуры в отопительных каналах одного простенка увеличиваются неравномерно по направлению с машинной к коксовой стороне и наоборот, температура со стороны выдачи кокса ниже, чем с машинной, или когда после загрузки угольной шихты в печную камеру парогазовые продукты разложения угля через трещины и неплотности кладки из камер попадают в отопительную систему – отопительные каналы и регенераторы?
Газ горит, плавятся насадки регенераторов, в печах образуются прогары и с каждой новой загрузкой все это повторяется.
Не лучше было, когда в отопительной системе тоже было давление, заглянуть в отопительный канал было невозможно. Воздух из регенераторов попадал в камеру. Поэтому коксовая батарея, которая должна служить 25 лет, выходила из строя через год – полгода.
Никто из заводских работников не мог найти причину, не хватало опыта, а иностранные исполнители советских заказов помалкивали.
В повести С.Н. Сергеева Ценского «Искать, всегда искать» есть глава «Загадка кокса», где один из героев справедливо замечает: «Копперс заинтересован в том только, чтобы сдать завод, годный к эксплуатации, а мы – в том, чтобы он нормально работал без перебоев». Но ведь дело тут было не только в перебоях, а в выходе из строя дорогостоящего оборудования и в том, что для домен не хватало кокса, который к тому же был плохого качества.
В 20-е гг. ХХ в. шли бурные дискуссии о судьбе металлургии Урала. Так знаменитый металлург В.Е. Грум-Гржимайло был убежден, что будущее Урала – в производстве высококачественного металла на небольших уральских заводах при использовании древесного угля, который можно получать, если не в кучах, то в специальных печах. Он считал, что отсутствие на Урале запасов коксующихся углей не позволит сооружать крупные металлургические предприятия.
Следует еще раз отметить, что способ коксования угля в кучах вообще не только на Урале дожил до середины ХХ в. Одному из авторов приходилось видеть коксовальные кучи в Индии еще в 1965 г. В них из угля получали, практически не кокс, а низкотемпературный полукокс для бытовых целей. Выход такого кокса из угля в «современных» углевыжигательных кучах составлял до 50%.
Однако был на Урале, ныне полностью выработанный, Кизеловский каменноугольный бассейн. В нем залегали прекрасные коксующиеся угли. Правда, они имели крупный недостаток – повышенное содержание серы. Но для выплавки, например, меди и других цветных металлов наличие серы в коксе не имеет значения.
Д.И.Менделеев в 1899 г. писал: «Для умножения массы металла в России, для его удешевления было бы очень важно, чтобы именно на Урале, началась выплавка чугуна на коксе. А для этого нет других, более подходящих, чем Кизел мест».
По-видимому, это его утверждение основывалось на том, что в конце 80-х гг. Х1Х в. на севере Пермской области (в Луньевке недалеко от г.Губаха и г. Кизел) были построены, для тех времен «современные», две коксовые батареи системы бельгийского инженера Эванса Коппе, без улавливания химических продуктов коксования. Они предназначались для коксования кизеловских углей. Но из-за большого содержания серы кокс не мог быть использован в черной металлургии и весь отправлялся на медеплавильный завод.
В 1913 г. в районе Экибастуза на копях, где в настоящее время крупнейший угольный разрез «Богатырь» начали строительство стойловых коксовых печей. Были получены первые партии кокса, которые на верблюдах доставлялись к железной дороге и отправлялись на металлургические заводы Урала. После революции эти опыты продолжил известный по Ленскому расстрелу, один из владельцев общества «Лена Гольдфилдс» концессионер Лесли Уркварт. Существовали проекты завоза на Урал «сибирского» кокса полученного из углей Кузнецкого и Черемховского каменноугольных бассейнов.
В архивах имеются сведения о просьбе владельцев Судженских (Кузбасс) и Черемховских (Восточная Сибирь) копей о снижении тарифов для перевозки кокса из углей этих месторождений на Урал.
После революции Совет труда и обороны РСФСР вернулся к рассмотрению вопросов развития уральской металлургии. В 1918 – 1921 гг. сибирским обществом инженеров в Томске, в котором участвовал знаменитый доменщик Курако, был разработан проект так называемого УКК (Урало-Кузнецкого комбината).
По этой идее, коксующийся уголь Кузнецкого угольного бассейна (Кузбасса) и даже кокс должны были идти на Урал, а в тех же вагонах в Сибирь и, в первую очередь, на проектируемый Кузнецкий металлургический комбинат – должна была поступать уральская железная руда в первую очередь с гор Благодать, Высокой, Магнитной. Коксовые печи намечалось строить самого современного по тем временам типа. Этот план претерпел некоторые изменения, после того как в Горной Шории недалеко от Кузнецка были также обнаружены значительные залежи железной руды.
В 1921 г. в план ГОЭЛРО было включено строительство металлургического завода с современным оборудованием на рудах горы Магнитной в районе станицы Магнитной Челябинской области. В 1925 г. в Свердловске было создано Уралпроектбюро, которое приступило к разработке предварительного проекта Магнитогорского завода. Помещалось бюро, преобразованное впоследствии в Востокгипромез, в здании сегодняшнего Екатеринбургского «Пассажа». 31 января 1929 г. в Свердловске создается управление по строительству Магнитогорского металлургического завода, в составе которого был предусмотрен коксохимический цех в из трех коксовых батарей по 63 печи в каждой, общей производительностью 656 тыс. т в год. Затем эта цифра была увеличена до 4 коксовых батарей производительностью до 1 млн т кокса в год.
В 1930 г. началось строительство самых современных, по тому времени высокопроизводительных коксовых батарей по проекту американской фирмы «Копперс». На этих коксовых батареях предусматривалось улавливание химических продуктов, которые образуются при коксовании угля. В составе завода предусматривались и цеха по переработке этих продуктов, то есть настоящее коксохимическое производство. 28 декабря 1931 г. первая коксовая батарея выдала кокс, а 17 апреля 1932 г. заработала и вторая.
Не обошлось и на знаменитой Магнитке без «модного» тогда вредительства, из-за которого в 1937 – 1938 гг. погибло столько специалистов. Так в журнале «За кокс Востока» (1932 г.), где освещались итоги пуска коксохимического производства отмечается: «Нельзя умолчать здесь и о том вредительстве классового врага, которое было выявлено на стройке коксохима. Сейчас классовый враг свою контрреволюционную работу особенно активно проявляет на гигантских стройках, вредя успешному завершению промышленной пятилетки.
В среду сынов деревни, сознательно и добровольно приехавших на Магнитострой с честной целью внести свой вклад труда на великом строительстве, не мог не проникнуть классовый враг. Проник он и на коксохим, и злостно вредил при его сооружении.
Мы отметим наиболее существенные акты его враждебных действий, своевременно выявленных или предупрежденных рабочими-ударниками, всюду бодрой и зоркой комсомолией или рабочими- строителями.
Вот примеры: в декантере были обнаружены умышленно заброшенные веревки, весом около 50 кг, на электропровода неоднократно забрасывались болты и проволока. Был случай пожара. По причинам его возникновения, явно определилось, что это дело рук классовых врагов на стройке и т.д. и т.п.».
Конечно, это все ерунда. Просто обычные строительные недоделки. Однако к 1938 г. в коксохимии (как и в остальных отраслях промышленности) было арестовано и, в большинстве случаев, расстреляно около 150 чел. И среди них почти вся высокопрофессиональная, талантливая «головка».
Косвенно или прямо эти репрессии можно проследить по журналу «Кокс и химия», подшивки которого сохранились в библиотеке Восточного научно-исследовательского углехимического института–ВУХИНа.
Даже простая статистика дает представление о масштабах бессмысленных репрессий.
В период с 1931 по 1938 гг. в журнале публиковались более 500 авторов и членами редколлегии были практически постоянно одни и те же 5 — 7 человек наиболее грамотных, знающих специалистов–коксохимиков в том числе начальник треста «Союзкокс» В.Ф. Логинов, главный инженер этого треста Р.А. Вальман, главный инженер Гипрококса Я.О. Габинский и др.
Просмотр журналов, находящихся, например, в библиотеке ВУХИНа (вероятно в 1937 г.) за три месяца издания 1931 г. было вырезано порядка 80 страниц, в 1932 г. 112 страниц, в 1933 г. — 40, в 1934 г. — 42, в 1935 г. — 36. В 1936 г. вырезали всего две страницы, в 1937 г. вырезанных страниц нет.
С 1931 по 1938 гг. уменьшается число вырезанных страниц, но остается большое число замазанных тушью фамилий. То есть, если сначала «вместе с автором» вырезали и статью, а с ней и соавторов, то в следующие годы только тушью замазывали фамилию. Причем, по-видимому, многое еще зависело и от квалификации «вырезальщика». Некоторые, «сильно грамотные», вычеркивали и вырезали из содержания фамилии на русском и иностранных языках (в те годы журнал «Кокс и химия» публиковал содержание на русском, английском и немецком языках). А в некоторых экземплярах вычеркнуты фамилии авторов только на русском языке.
Вычеркивались фамилии авторов и из проспектов будущих статей и изданий, вырезался весь проспект или содержание будущего журнала. Зачеркивали также фамилии в литературных ссылках.
Внимательные «бдительные» цензоры читали текст «от корки до корки».
Так, вычеркнуты названия некоторых заводов, например «завод имени Рыкова». С 1936 г. вообще избегали печатать названия заводов по городам и рабочим поселкам, а стали писать: завод № ...., видимо, «от греха подальше», так как названия многих городов и рабочих поселков Донбасса и Приднепровья именовались по фамилиям вождей, которых репрессировали. Да что вожди? В одной из статей вычеркнута фамилия даже знаменитого русского химика А.Е.Чичибабина. За то, вероятно, что он был так называемый «невозвращенец».
А один из авторов этой книги и многие другие в конце 40-х гг. уже учили органическую химию по Чичибабину. И какой это был учебник! Уж скучным его точно не назовешь!
С 1935 г. начала «убывать» редколлегия. В 1937 г. редколлегии вообще нет. Журнал подписывал технорук Петров, а в 1938 г. врид отв. редактора.
Автору известно это потому, что он был знаком с К.Н. Клопотовым, который — единственный из всех членов редколлегии с 1931 г. — остался живым. Он тоже «посидел», но недолго, и в издании «Общей химической технологии топлива» (1940 г.) был редактором этого очень солидного учебника. Жаль, что большинство библиотек его списали и уничтожили, К.Н. Клопотов пережил в эвакуации войну и «умер в своей постели».
Главный редактор журнала, управляющий трестом «Союзкокс» В.Ф.Логинов, главный инженер треста Р.А. Вальман, управляющий трестом «Коксохиммонтаж» Г.А. Яновский и многие другие члены редколлегии журнала были арестованы и расстреляны.
Некоторые авторы, те, которых арестовывали в 1930 г. по делу «Промпартии», были освобождены после относительно небольшой «отсидки» и работали в промышленности. Их фамилии в 1932 — 1938 гг. не вычеркивались
Профессор Я.О. Габинский — один из создателей журнала «Кокс и химия», высоко эрудированный специалист именно в области технологий переработки угля. Бессменный (до 1937 г.) научный редактор журнала; практически в каждом журнале появлялись статьи и обзоры Я.О. Габинского.
Им написаны несколько монографий и главный, к сожалению, незаконченный труд «Курс коксового производства»: капитальный учебник с очерком по истории коксохимической промышленности, в основу которого легла статья Я.О. Габинского в журнале «Кокс и химия» в 1935 г.
Это год, который многими авторами считается 200-летием начала коксохимической, точнее коксовой промышленности, так как в 1735 г. английский промышленник Авраам Дерби осуществил успешное применение каменноугольного кокса в доменной плавке. Кстати, в 1985 г., к сожалению, в журнале «Кокс и Химия» нет ни одного материала, посвященного 250-летию этого серьезного технического рубежа.
Несмотря на то, что улавливание химических продуктов коксования ведет технологическое начало с середины Х1Х в., все- таки началом коксохимии можно считать действительно 1735 г.
В учебнике Я.О. Габинского приведены также биографии и даже портреты известных зарубежных и отечественных инженеров и ученых, которые внесли большой вклад в развитие коксохимической промышленности (Эванс Коппе, Генрих Копперс, Огго, Грум-Гржимайло и др). Издание отпечатано практически на газетной бумаге, но в нем приведено большое число фотографий, чертежей и схем конструкций коксовых печей. Освещен зарубежный и частично отечественный опыт технологии эксплуатации коксовых печей.
Капитально обсуждаются теоретические вопросы анализа особенностей процесса коксования, свойства углей, теоретические основы шихтования углей для получения качественного кокса.
К большому сожалению, успел выйти только один том двухтомного издания, посвященный производству кокса. Второй том, в котором должны были быть отражены вопросы технологии улавливания и переработки химических продуктов коксования, не вышел по тем же известным «вычеркнутым» причинам.
Г.А. Яновский — управляющий трестом «Коксохиммонтаж». Под его руководством уже в 1934 г. была пущена первая коксовая батарея, построенная по чертежам Гипрококса, из отечественного огнеупора и полностью нашими рабочими и инженерами. Расстрелян и реабилитирован.
Профессор Г.Л. Стадников. Вот к кому вполне применимо понятие — корифей углехимии. Автор многих статей и монографий по происхождению и строению углей, теории хранения углей и их самовозгорания. Один из основных авторов журналов «Химия твердого топлива», «Кокс и химия». Автор не только теорий коксования углей, но и теорий процессов, происходящих при термическом разложении дерева и торфа. Был ведущим сотрудником Института горючих ископаемых. Арестован в 1938 или 1939 г., «сидел» на Воркуте, работал в так называемой «шарашке». Дожил до освобождения и реабилитации. Затем снова активно работал в Институте горючих ископаемых. На одном из заседаний Ученого совета института «скромно» задал докладчику 25 вопросов — естественно, по делу!
Журнал «Химия твердого топлива» отметил 70 и 90-летние юбилеи Г.Л. Стадникова. «Вычеркнутый» автор М.Л.Френкель удален из статей, относящихся к вопросам пуска коксовых батарей. То, что он автор и соавтор статей на эту тему — неудивительно, так как М.Л. Френкель был создателем и руководителем пускового отдела треста «Коксохиммонтаж», из которого впоследствии выросла Теплотехстанция, затем преобразованная в Коксохимстанцию.
Пусковым отделом под руководством М.Л.Френкеля были разработаны и осуществлены на практике основные принципы разогрева и пуска коксовых батарей, которые обеспечивали разогрев коксовой батареи без каких-либо серьезных повреждений кладки коксовых печей.
Отсидев в Норильске, и, будучи после смерти Сталина освобожден и реабилитирован, работал начальником технического отдела коксохимического производства Нижнетагильского металлургического комбината.
Е.Э.Лидер. Участник строительства Магнитки и Губахи. Арестован, сидел, но был освобожден в 1939 г. После Великой Отечественной войны заведовал кафедрой «Пирогенных процессов» (Химическая технология твердого топлива) в Московском химико-технологическом институте им. Д.И. Менделеева. Автор и соавтор идеи применения кольцевой печи для коксования углей.
В 1933 — 1937-х гг. в журнале появляется много статей, упоминаний в статьях о так называемом «вредительстве» на производстве.
С учетом опубликованных материалов о положении дел и в других отраслях промышленности автору представляется, что масштабы этого «вредительства» сильно преувеличены. Просто на производстве работали плохо обученные люди.
К 20 сентября 1934 г. первая очередь коксохимического производства теперь уже Магнитогорского металлургического комбината (ММК) в составе 4 коксовых батарей работала полным ходом. К началу войны было 5 батарей, а в 1945 г. их было 8. В 70-е гг. составе коксохимического производства ММК работало 14 коксовых батарей.
Практически одновременно со строительством первенца уральской коксохимии на Урале строились и другие коксохимические заводы. Так в 1929 г. в центре Кизеловского угольного бассейна городе Губаха Пермской области началось строительство Губахинского коксохимического завода.
Правда, по-старому, практически дореволюционному, проекту строились устаревшие шамотные малопроизводительные коксовые батареи по 47 печей, не то что в «Магнитке», но на них уже было улавливание химических продуктов коксования. Проект углеобогатительной фабрики был еще немецкий – фирмы «Гумбольдт», но коксовые батареи проектировал уже существовавший тогда «Мосгипрококс».
5 декабря 1936 г. на Губахинском коксохимическом заводе был выдан первый кокс, и заработали установки по улавливанию химических продуктов коксования.
Практически одновременно с пуском «Магнитки» в 1931 г. было принято решение о строительстве Ново-Тагильского (в отличие старого демидовского) металлургического завода и Нижне-Тагильского коксохимического завода, который с 1956 г. вошел в состав металлургического комбината (НТМК) в качестве коксохимического производства.
Поскольку приоритет все время отдавался прославленным первенцам пятилеток – Магнитке и Кузнецку, строительство в Нижнем Тагиле велось значительно медленнее. Первая коксовая батарея выдала кокс только 17 июня, а вторая 20 октября 1940 г. Всего должно было быть построено 4 высокопроизводительных коксовых батареи системы «Беккер-Гипрококс» на основе американской конструкции.
Строительство коксохимических производств на Урале привязывалось обычно к нуждам металлургов. Существовал стереотип: одна доменная печь – одна коксовая батарея. Но доменные печи работали все производительнее и коксовое производство должно было расширяться.
В конце 30-х гг. было принято решение о строительстве Челябинского металлургического завода спецсталей с коксохимическим производством и строительство такого же завода вблизи г. Орска Оренбургской области. Челябинский и Орско-Халиловский, которые стали металлургическими комбинатами, предполагались для получения качественных сталей, что определялось наличием полиметаллической рудной базы. Но по известным причинам (началась война) строительство этих заводов было временно отложено.
Для обеспечения крупнейшего города и промышленного центра Урала газовым топливом проектировалось сооружение крупного Свердловского коксогазового завода в районе озера Шувакиш.
Несмотря на тяжелые военные обстоятельства к 1945 г. в Нижнем Тагиле работало уже 4 коксовых батареи, на Магнитке 8. В 1943 г. возобновилось строительство коксовых батарей в Челябинске, и 2 августа 1944 г. батарея выдала первый кокс, причем на коксовой направляющей в огне сгорело чучело Гитлера.
В 1943 г. было начато строительство коксохимического производства на Орско-Халиловском металлургическом комбинате, и 5 ноября 1950 г. первая коксовая батарея дала кокс. Затем, практически каждый год в строй вводилась новая коксовая батарея. Одновременно с комбинатом вблизи города Орска Оренбургской области вырос и новый город – Новотроицк.
В связи с таким быстрым (т.е. нормальным) строительством коксовых батарей и отставанием строительства доменных печей ( к пуску последней по первоначальному плану четвертой коксовой батареи еще не была готова ни одна доменная печь) образовался излишек кокса, который, в частности, был направлен на строящийся Руставский металлургический завод в Грузии, где наоборот, должны были пускать доменную печь, а строительство коксовой батареи отставало.
В связи с этим вспоминаются казусы плановой экономики. Кокс для Рустави был запланирован из углей более высокой сернистости (грузинские и донецкие угли), чем получался на Орско-Халиловском коксохимическом предприятии. В связи с этим Руставскому заводу пришлось уплатить значительную сумму за малосернистый кокс Орско-Халиловскому, хотя это и не вызвало никаких усилий со стороны уральских коксохимиков.
Зато они пострадали в 70-х гг., когда, в связи с крупной аварией, из строя вышла Беловская (Кузбасс) центральная обогатительная фабрика, поставлявшая уральским заводам основу угольной шихты для получения качественного металлургического кокса – коксовые и жирные угли.
Правительством немедленно были приняты меры и из Донбасса направлены на Урал эшелоны углей этих марок. С серой в донецких углях уральцы справились. А вот из-за более низкого содержания азота в донецких углях по сравнению с кузнецкими, уральцы не смогли произвести нужное количество удобрения – сульфата аммония. Ну, нет азота в угле, не из чего сделать продукт. Но плановую экономику это не интересовало. И уральцы не получили премию за два месяца (конечно только ИТР). Нет продукции, нет и премии. И такие казусы иногда случались.
К 1975 г. в Уральском экономическом районе работало 40 коксовых батарей и Уральский экономический район, пережив, как и вся страна, годы перестройки, продолжает оставаться главной составляющей коксохимической промышленности России. В 2005 г. коксохимический потенциал Урала – это 32 современных коксовых батареи, которые по мере износа постоянно обновляются на более высоком техническом уровне.